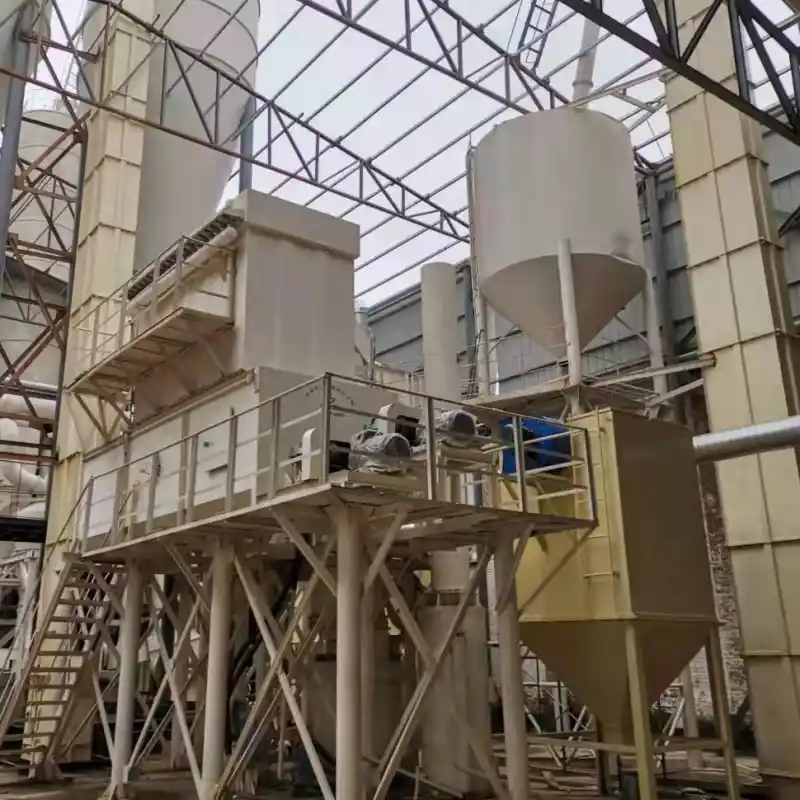
Revolutionary Optimization Design for Ultra-Efficient Digestion System in High-Specific-Surface Calcium Hydroxide Equipment
In the production process of high specific surface calcium hydroxide, the digestion system occupies a core position. Its core task is to promote the reaction of quicklime (CaO) with water to produce calcium hydroxide (Ca (OH)₂). The quality of this reaction process not only has a direct impact on the output and quality of the product, but is also closely related to the energy consumption and environmental protection indicators in the production process. Therefore, optimizing the design of the digestion system is of great significance to improve the production efficiency of high specific surface calcium hydroxide.
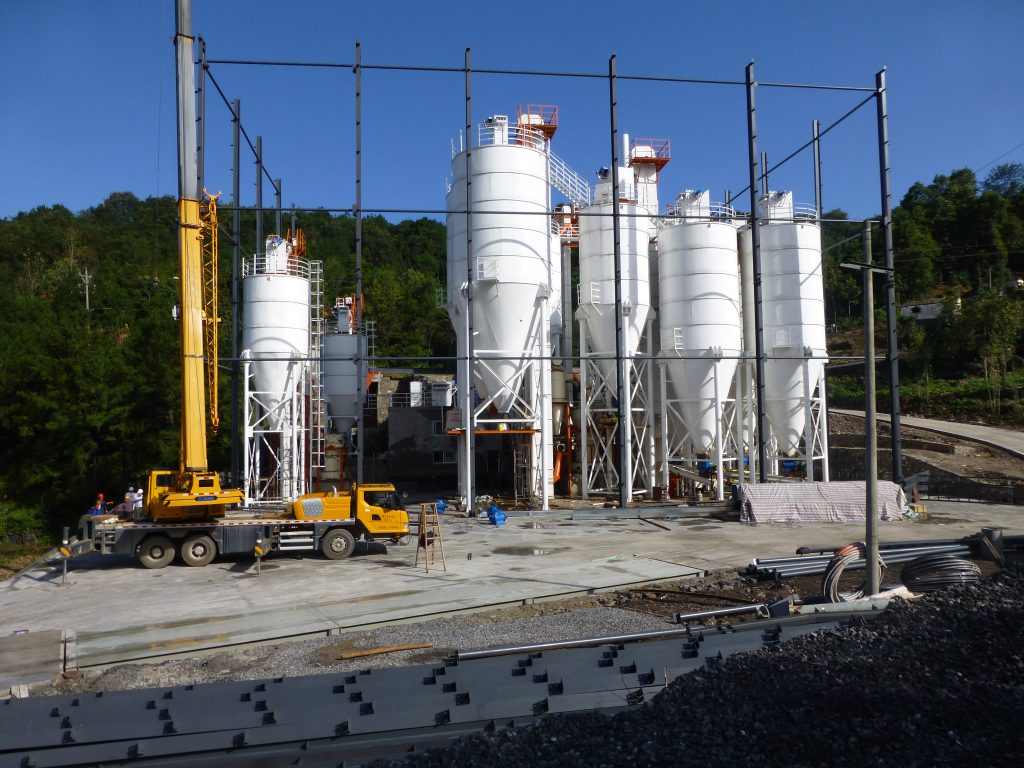
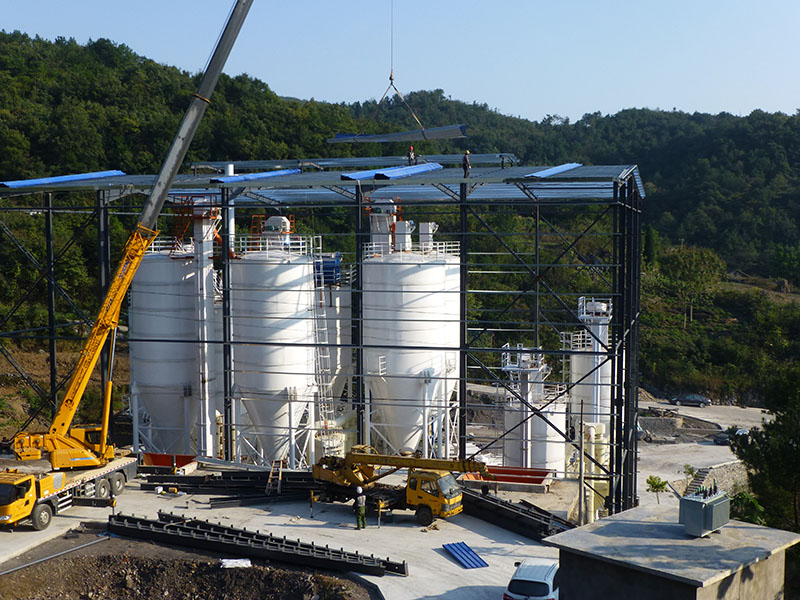
Limitations of traditional digestion systems
Poor reaction efficiency: In the past, common digesters were mostly simple-structured stirring tanks. In this type of digester, quicklime and water cannot be evenly blended during the mixing reaction, which ultimately makes it difficult to complete the digestion process.
High energy consumption: Due to the poor thermal efficiency of traditional equipment, a large amount of energy is consumed in the digestion process, which undoubtedly greatly increases production costs.
Dust and heat emission issues are prominent: Traditional equipment lacks effective control measures when dealing with dust and waste heat generated during the reaction process, and it is difficult to meet the current strict environmental protection requirements.
Advantages of chain-type stirring digester
In order to break through the bottleneck of traditional digestion systems, Guikuang has carried out all-round optimization work on the design of digestion systems and successfully developed a chain-type stirring digester with independent intellectual property rights. Compared with traditional equipment, Guikuang’s digester has significant advantages in efficiency, environmental protection and intelligence.
Innovation of the mixing system
Adopting an innovative chain mixing structure: With this unique structure, quicklime and water can be fully mixed, allowing the reaction to proceed more thoroughly.
Carefully optimized mixing blades: From shape design to material selection, it has been optimized, which not only effectively reduces the degree of wear of the equipment, but also greatly extends the service life of the equipment.
Optimization of heat energy utilization and heat dissipation control
Introducing a waste heat recovery mechanism: Through this system, the heat released during the reaction process can be recycled and utilized for heating raw materials or heating the factory, greatly improving the efficiency of energy utilization.
Equipped with an efficient heat dissipation module: This module can effectively avoid the occurrence of local overheating, thereby preventing adverse effects on equipment and product quality.
Realization of intelligent control
Equipped with an automated control system: the system can accurately control key parameters such as water-cement ratio, reaction time and temperature.
With online monitoring and data analysis: through real-time monitoring and data analysis, the stability and controllability of the production process are significantly improved.
Significant improvement in environmental performance
Installation of high-efficiency dust removal equipment: can efficiently capture dust generated during the reaction process.
Adopting a closed design: effectively reducing the spillage of gas and dust, and reducing pollution to the environment.
The optimized design of the digestion system of the high-specific calcium hydroxide equipment is the key to achieving the production goals of high efficiency, energy saving and environmental protection. Through comprehensive upgrades in the mixing system, heat energy utilization, intelligent control and environmental protection performance, the modern digestion system far exceeds the performance of traditional equipment.